Product description
Technical indicators
Voltage and frequency PH/3PHAC220V50/6OHz3PHAC380V50/60Hz
Allowable voltage 220V:170V~240V;380V:330V~440V
Voltage 220V:0~220V;380V:0~380V
Frequency 0.1400.0Hz
Control mode VF control
Display 4-digit digital tube display, indicator display, display set frequency, output frequency, output current, DC bus, etc.
Control Characteristics
Output frequency Fan circle 0.1400.0H
Frequency setting fraction Digital setting 0.10Hz Analogue setting: 0.1% of maximum output frequency
Output frequency accuracy 0.1Hz
VIF control The V/F curve can be set arbitrarily to meet the needs of various loads.
Torque control Auto boost: automatically determine the torque boost according to the load condition; manual boost: 0.0~20.0% torque boost can be set.
Multi-functional input terminals 4 multi-functional input terminals for 15-segment speed control, 4-segment acceleration/deceleration switching for programme operation, UP/DOWN function, emergency stop and other functions.
Multi-function output terminal 1 multi-function output terminal for indication and alarm output of running, zero speed, external abnormality, programme operation, etc.
Acceleration/deceleration time setting Acceleration/deceleration time can be set separately from 0 to 999.9s.
Other Functions
PID control Built-in PID control
RS485 Standard RS485 communication function (MODBUS)
Frequency setting Analogue 0~10V, 4~20mA, direct setting from keyboard, RS485 setting, UP/DOWN setting, etc.
Note: AVI terminal can be selected by toggle switch for analogue voltage input (0~10V) and analogue current input (4~20mA)
Multi-Segment Speed 4 multi-functional input terminals can form 15-segment speeds.
Automatic voltage stabilisation Automatic voltage stabilisation can be selected as required
Counter Built-in 2 sets of counters
Protection function
Overload protection Constant torque 150%/1 min, alternating torque 120%/1 min.
Overvoltage protection Overvoltage protection can be set
Undervoltage protection Undervoltage protection can be set
Other protections Short-circuit protection, over-current protection, parameter locking, etc.
Ambient temperature -10℃ to 40℃.
Ambient temperature -10℃ to 40℃ (no freezing)
Ambient humidity below 95% (no condensation)
Altitude 1000m or less [more than 1000m need to downgrade use].
Vibration 0.5G or less
Cooling method Forced air cooling
Protection class IP20
Installation method Wall-mounted, standard 35mm rail mounting (below 5.5kw)
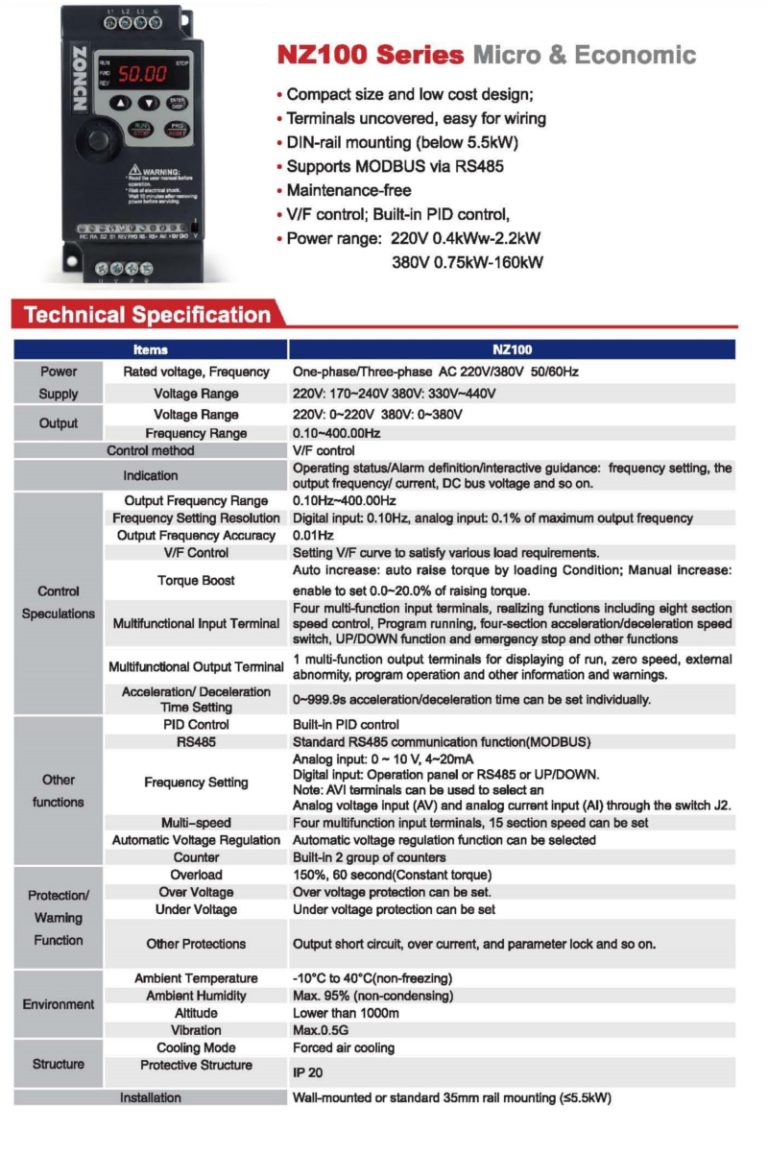
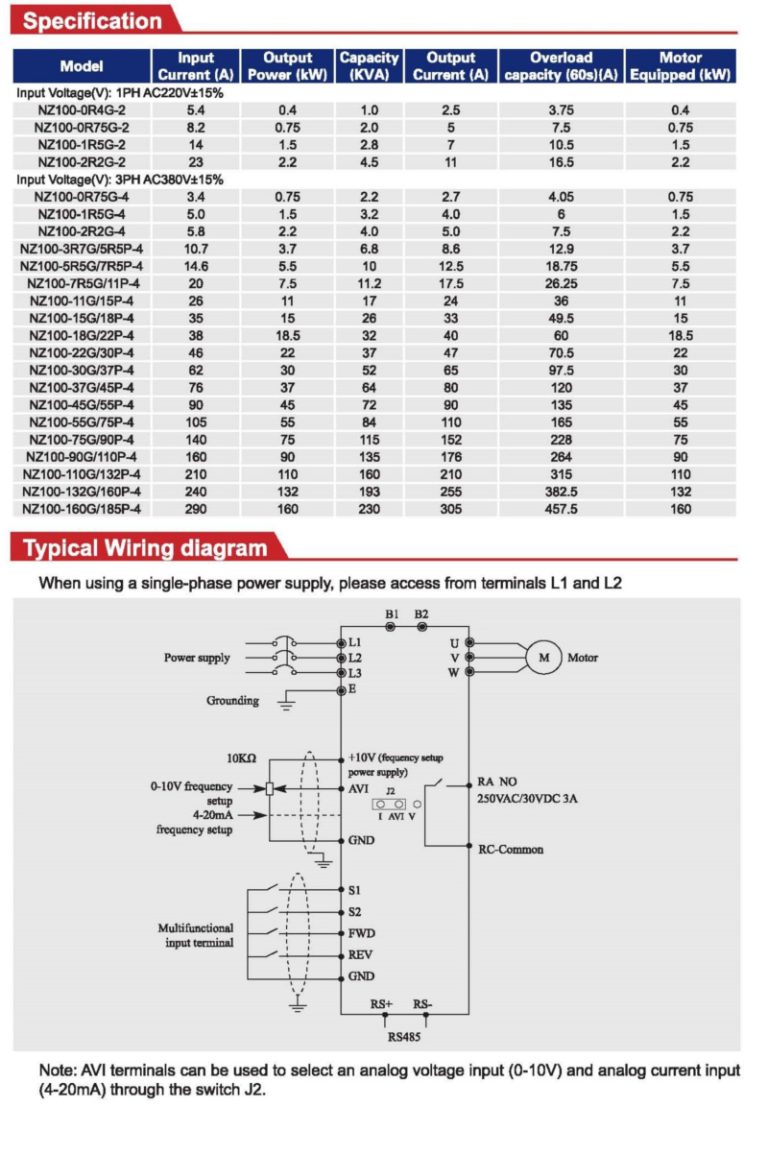
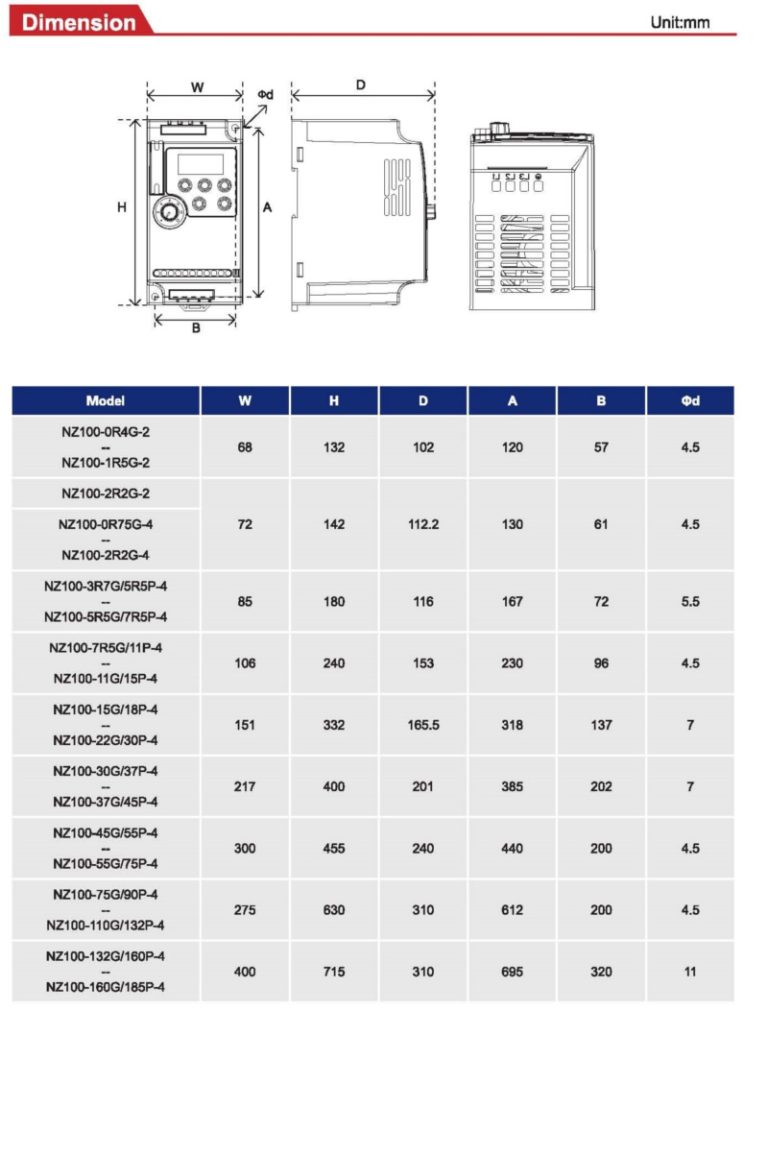
FAQ
What is the Advantage and Disadvantage of Frequency Converter?
Variable Frequency Drives (VFDs) offer a wide range of advantages in many industrial and commercial applications, but there are also some disadvantages. Here are the detailed advantages and disadvantages of frequency converters:
One of the most significant advantages of a VFD is the ability to adjust the speed of the motor as needed. This significantly reduces energy consumption, especially when the load varies, compared to traditional on/off control methods. It is particularly suitable for fans, pumps and other equipment that require variable speed control.
Frequency converters allow the operator to precisely adjust the motor speed as needed. This allows for more precise process control and improved product quality. A variety of built-in protections, such as overcurrent, overvoltage, and overheating protection, effectively protect the motor and the inverter itself.
Inverters are expensive to purchase and install, especially for high-power equipment. Additional accessories such as filters, radiators, etc. may be required, increasing the overall cost. They also generate noise during use and may produce electromagnetic interference that affects surrounding electronic equipment, requiring shielding and grounding measures.
Frequency converters offer significant energy savings, precise process control and versatility, but they also suffer from high initial costs, increased complexity, harmonics and electromagnetic interference. When selecting and using a frequency converter, it is necessary to comprehensively consider its advantages and disadvantages, and weigh them according to specific application scenarios and needs.