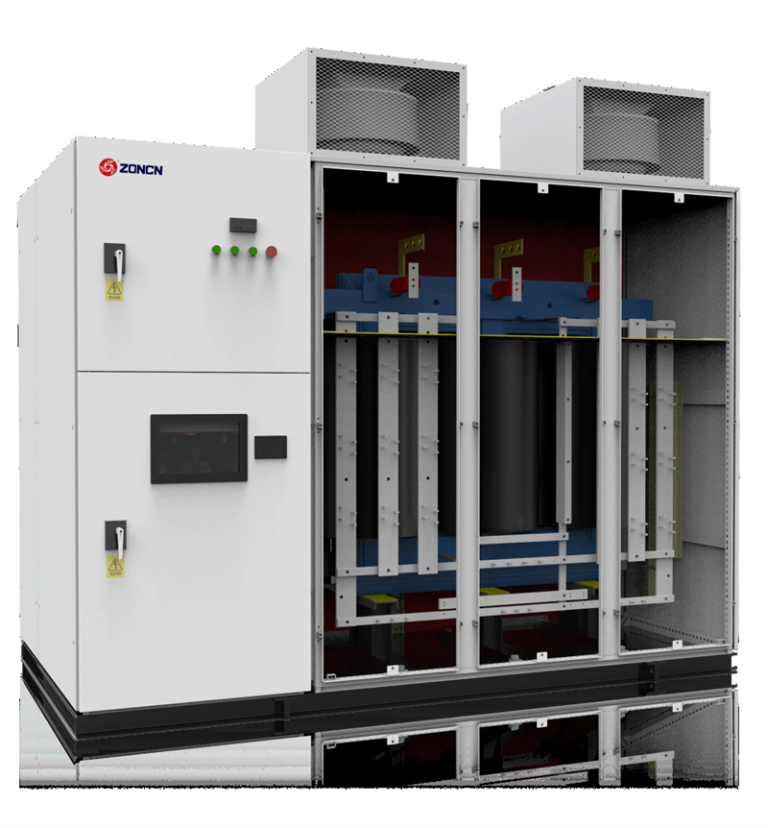
Customers need to configure a high-voltage frequency converter for air-cooled screw machines, and ZONCN recommends ZCH100 as the high-end frequency converter. ZCH100 series high-voltage frequency converter adopts the form of multi-level “high-high” voltage source of power units in series, i.e., it adopts a number of low-voltage PWM inverter power units in series to connect the high-voltage input to the power unit inverter superimposed on the direct high-voltage output after passing through the phase-shifting transformer, without the need of bucking, boosting and filtering devices. Transformer to the power unit inverter superimposed on the direct high-voltage output, without the need for step-down, boost and filtering devices, can be in the input voltage for the rated voltage range of ± 10% of the long-term reliable continuous operation. It adopts advanced IGBT power semiconductor devices, precise AC drive control, multi-level output control and other technologies, so that the ZCH100 high-voltage drive products have excellent control performance and high reliability.ZCH100 is widely used in rolling mills, conveyor belts, fans, test platforms, and compressors, etc., in order to drive constant-torque loads or square-torque loads, so as to achieve the purpose of precise control and energy saving. The ZCH100 is widely used in rolling mills, conveyor belts, fans, test rigs, and compressors to drive constant torque or square torque loads for precise control and energy savings.
ZCH100 AC drive system consists of power input and output units, matching capacitors, air-cooling devices and so on. The system has a very high working capacity; the frequency conversion device has a high power factor, which improves the quality of power; the frequency conversion device has a high efficiency, small heat generation, reducing the space occupied by the equipment, effectively reducing the total amount of investment in the project, and maximising the saving of power and investment for the user;
Phase shifting transformer and multi-level technology make the output waveform smooth, low du/dt and common mode voltage, no need for output filter and common mode voltage filter, the output current and voltage waveform curve is close to sinusoidal, and the harmonic content is very low. It effectively suppresses the impact of high harmonics on the power grid, motor and motor cable, so that it meets the requirements specified in the electromagnetic harmonic specification.
The mature multi-level control algorithm enables precise vector control of the motor, achieving high performance with excellent cost control.The ZCH100 has a standard HMI and logic controller, which provides on/off control of high voltage circuit breakers, status monitoring; input power supply and motor operation status monitoring; as well as process monitoring from user-defined processes.
As ZCH100 itself has very strong communication function, it can use Modbus TCP/IP or profinet protocol to communicate with the master PLC, and the HMI realises the control parameter setting of the drive control system and the graphic and data display of the whole process of the system; it can also communicate with the upper control system through the area bus adapter to realise the monitoring of the whole process system. Therefore, it is also an ideal choice for high-pressure transmission products in large-scale process control systems.
Installation topology diagram
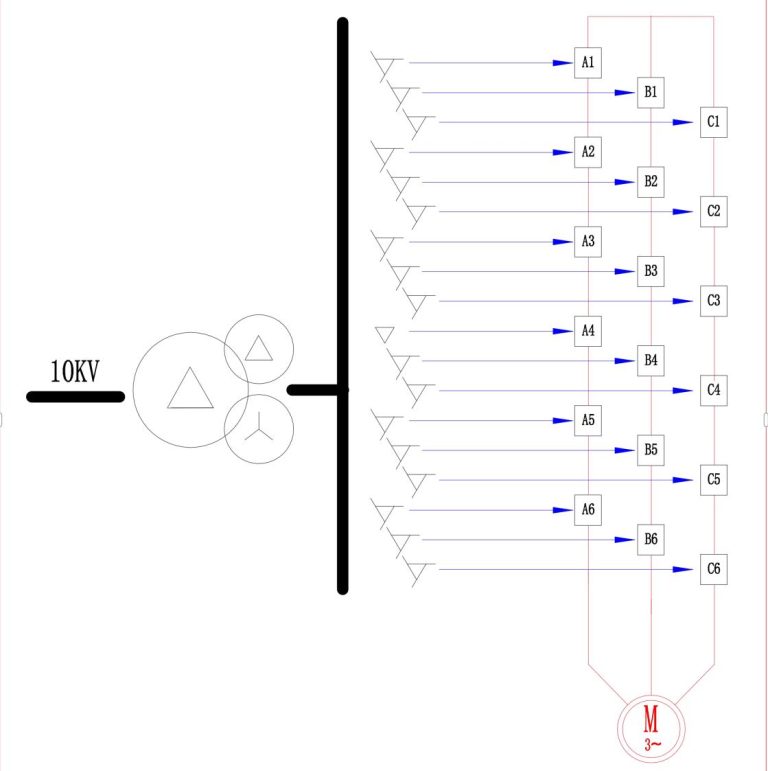
Main circuit wiring diagram
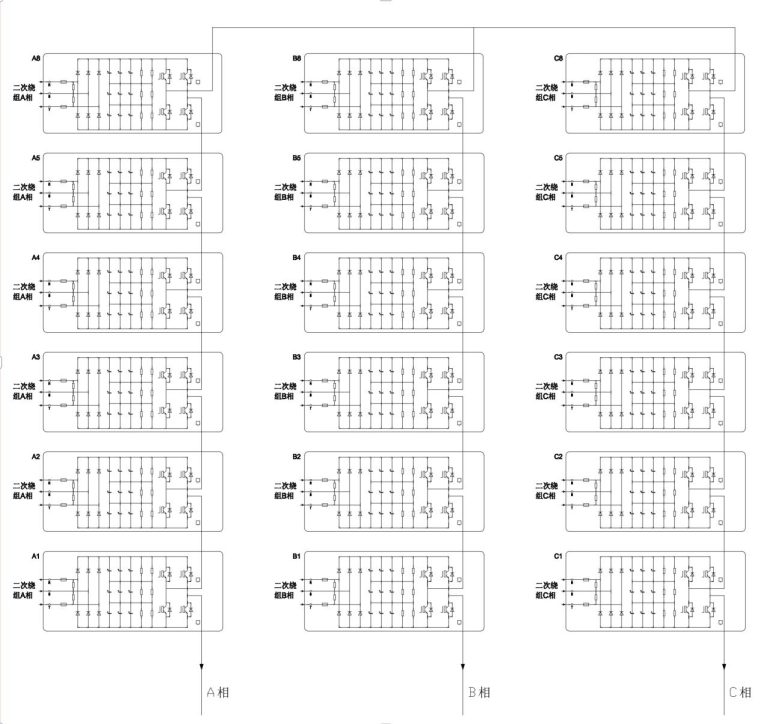
Superior performance of ZCH100
High torque output
The torque output of a motor driven by the ZCH100 is able to obtain the rated torque of the motor at low speeds without the need for feedback from a rotary encoder or speed measuring motor.
Flux optimisation
In optimised mode, the motor flux is automatically adapted to the load to improve efficiency while reducing motor noise. Thanks to flux optimisation, the total efficiency of the inverter and motor can be increased by 1% to 10%, depending on the load.
Speed Jump Setting
Mechanical systems may face resonance problems at certain speeds or speed bands. To avoid operating at these speeds, the ZCH100 software has up to 5 different speed settings to avoid operating at these speeds. Each speed band has an upper and lower trigger point and as the system passes through this speed band, the inverter is forced to accelerate or decelerate to an adjacent higher or lower speed to enter the permitted operating range of stable operation, thus minimising mechanical resonance problems.
Resonance suppression
In applications where the system may be stabilised at dangerous speeds, the usual solution is to change the mechanical design, which is time-consuming and adds to the investment costs. The ZCH100 has special torque resonance suppression software for this situation. By applying a given consumption 180 degrees inverse to the sensed oscillating torque, the impending resonance can be quickly reduced. Precision Speed Control The dynamic speed error of the VF control is 0.4%s in open-loop applications and 0.1%s in closed-loop applications. vector control inverters are greater than 0.8%s in open-loop and 0.3%s in closed-loop.
Precise torque control
Dynamic torque step response time can reach 1~5ms in open loop application, while vector control inverter needs 10~20ms in closed loop and 100~200ms in open loop.
Carrier frequency setting
Due to the operating characteristics of IGBT, high power transmission is not suitable for high carrier frequency operation, which will lead to a significant increase in power consumption and temperature. The carrier frequency setting is limited to 2K.
In this programme ZCH100 high-voltage frequency converter perfect integration of the actual product applications, not only to retain the original product device also upgraded the efficiency of the product, it can be said that the results of a one-two punch, if you have any demand for frequency converter products are welcome to contact us.