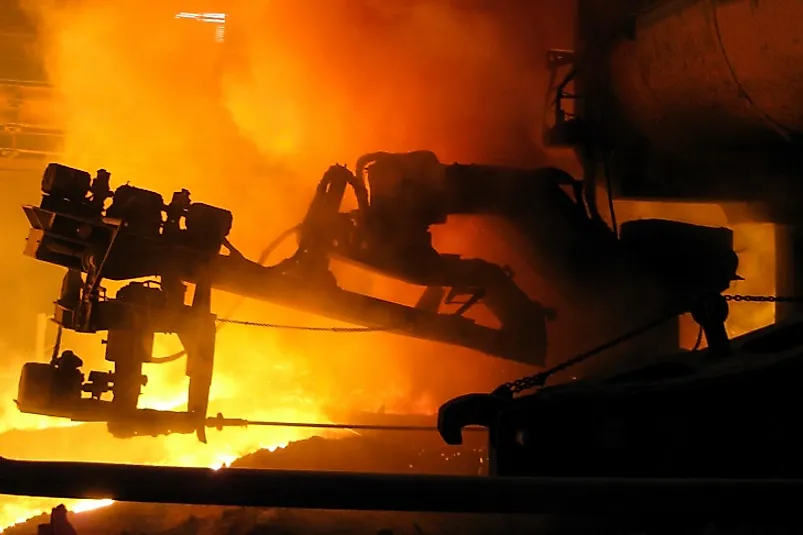
Power Inverter is a device that converts industrial frequency power supply (50Hz or 60Hz) into AC power supply of various frequencies to realize variable speed operation of motor. The control circuit completes the control of the main circuit, the rectifier circuit converts AC power into DC power, the DC intermediate circuit smoothes and filters the output of the rectifier circuit, and the inverter circuit converts DC power into AC power. For inverters that require a lot of calculations, such as vector control inverters, sometimes a CPU for torque calculation and some corresponding circuits are also required.
In steel mills, some important fans and pumps, such as steelmaking dust removal fans, blast furnace dust removal fans, sintering waste heat fans, cold rolling hydrogen compressors, boiler feed water pumps and other equipment, are usually driven by AC asynchronous motors. These equipment have a wide speed regulation range and have a greater impact on the process and environmental protection. In the early days, most of the fans and pumps in steel mills did not regulate speed. They directly used industrial frequency power supply and constant speed drive. By adjusting the damper and valve to control the air volume and water supply, the energy was also wasted. If high-voltage frequency converters are used for variable frequency speed regulation, a large amount of electricity can be saved and benefits can be brought to the enterprise. In addition, the power of large fans in steel mills, such as blast furnace blowers, sintering main exhaust fans and oxygen generators, is relatively large. They are generally driven by synchronous motors and can also be transformed by variable frequency speed regulation.
High-voltage frequency inverters are widely used in the smelting industry. Their main function is to control and adjust the speed and voltage of the motor to meet various needs in the smelting process. Typical applications: slurry pumps, induced draft fans, descaling pumps, ventilation fans, dust removal fans, centrifugal feed pumps, blast furnace blowers, etc. The following are some of the main applications of high-voltage frequency converters in the smelting industry:
Motor control: Various motors used in the smelting process (such as fans, water pumps, compressors, etc.) usually need to adjust the speed and power according to production needs. High-voltage inverters can accurately control the speed and torque of the motor to achieve energy saving and flexibility in the production process.
Electric furnace control: In the smelting process, the electric furnace is one of the common equipment used to melt metals and alloys. High-voltage inverters can control the heating rate and temperature of the electric furnace to ensure that the metal material in the furnace reaches the required melting temperature, and can perform precise temperature adjustment when necessary.
Rolling mill control: In metal processing, the rolling mill is a common equipment used to roll metal billets into the desired shape and size. High-voltage inverters can control the roller speed and pressure of the rolling mill to ensure that the metal billets obtain the ideal shape and size during the rolling process.
Fan and exhaust system: Smelters are usually equipped with a large number of fans and exhaust systems for ventilation, flue gas treatment and exhaust gas emission. High-voltage inverters can adjust the operating speed of fans and exhaust systems to meet the ventilation needs under different process conditions and improve energy efficiency.
Water pump system: In the smelting production process, a large amount of water resources are required for cooling, cleaning and transportation. High-voltage inverters can control the flow and pressure of the water pump system to meet the water resource needs of different process stages and improve the utilization efficiency of water resources.
In the metallurgical industry, inverters are needed to drive high-power and high-flow equipment, and the stability of inverters is further improved. High-voltage inverters play a key role in the smelting industry. Through precise motor control and regulation, they improve the efficiency, flexibility and energy efficiency of the production process, while reducing production costs and environmental pollution.