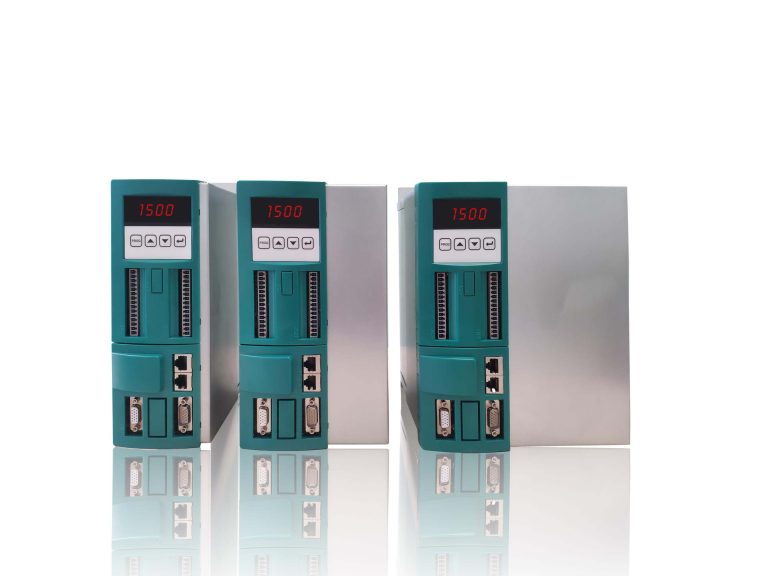
Before the frequency converter adjusts the water pump pressure, we must first understand the working principle and performance parameters of the water pump. A water pump is a device that converts mechanical energy into liquid pressure energy. Its working principle is to use the rotation of the impeller to generate centrifugal force to suck the liquid from the inlet and discharge it from the outlet. The performance parameters of the water pump mainly include flow, head, power, efficiency, etc.
The working point of the water pump refers to the point where the water pump can work normally under a specific flow and head. The following factors need to be considered to determine the working point of the water pump:
System requirements: Determine the required flow and head according to the system requirements.
Pipeline resistance: Calculate the resistance loss of the pipeline according to factors such as the length, diameter, and material of the pipeline.
Pump characteristic curve: According to the pump characteristic curve, determine the power and efficiency of the pump under the required flow and head.
Choosing a suitable frequency converter is the key to adjusting the water pump pressure
The main function of the frequency converter is to adjust the speed of the motor, thereby changing the flow and head of the water pump. When choosing a frequency converter, you need to consider the following factors
Power: The power of the frequency converter should match the power of the water pump.
Voltage: The input voltage of the frequency converter should be consistent with the grid voltage.
Frequency range: The output frequency range of the frequency converter should be able to meet the working requirements of the water pump.
Control mode: The control mode of the frequency converter should match the control requirements of the water pump, such as PID control, constant pressure control, etc.
Install the inverter
Install the inverter correctly into the electric control cabinet and ensure that the power supply, motor and control lines are correctly connected.
Set the inverter parameters
After connecting the inverter and the water pump, you need to set the inverter parameters to meet the working requirements of the water pump.
Frequency setting: Set the output frequency of the inverter to adjust the speed of the motor.
Acceleration and deceleration time: Set the acceleration and deceleration time of the inverter to avoid shock when the motor starts and stops.
PID parameters: If PID control is used, PID parameters need to be set, such as proportional coefficient, integral time, differential time, etc.
Protection parameters: Set the inverter’s overload, overheating, overvoltage and other protection parameters to ensure the safe operation of the system.
Debugging the pump pressure
During the initial operation, debugging is required:
- Start the inverter: Start the inverter and gradually increase the frequency, observe the operation of the pump and the system pressure.
- Adjust PID parameters: If the PID control mode is used, adjust the PID parameters according to the system response to ensure that the pressure is stable near the set value.
- Monitoring system: After running for a period of time, monitor the system pressure, flow and inverter operation status to ensure that everything is normal.
- Optimize system performance
After debugging the pump pressure, the system performance can be further optimized. For example, adjust the PID parameters, optimize the pipeline design, and regularly inspect and maintain the pump and inverter to ensure the long-term stable operation of the system.
In the process of adjusting the pump pressure, pay attention to the following points:
Safe operation: When operating the inverter and the pump, ensure safety and avoid electric shock and mechanical injuries.
System matching: Ensure that the parameters of the inverter and the pump match to avoid equipment damage caused by parameter mismatch.
Environmental factors: Consider the impact of environmental factors such as temperature and humidity on the pump and inverter.
Energy saving and consumption reduction: Under the premise of meeting the system requirements, try to reduce the operating frequency of the water pump and reduce energy consumption.
Through the above steps, the pressure of the water pump can be effectively adjusted to meet the needs of the system. At the same time, by optimizing system performance and paying attention to safe operation, the long-term stable operation of the system can be ensured.