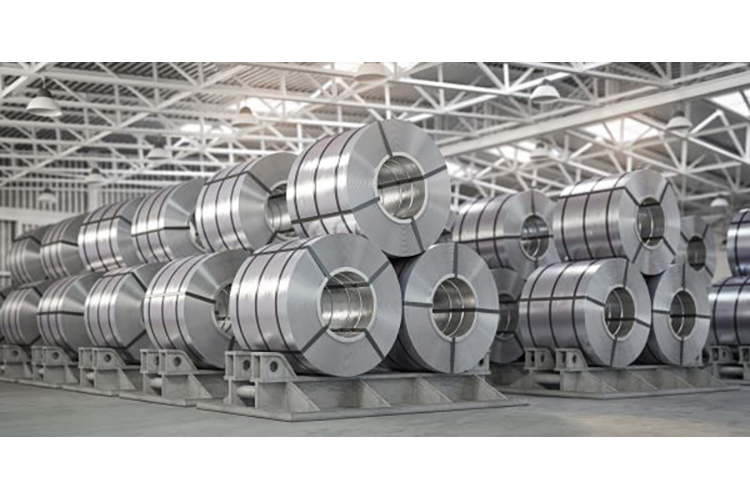
The application principle of high-voltage inverters in the non-ferrous metal industry involves power control and frequency regulation technology. In the non-ferrous metal industry, different production processes and equipment require different operating speeds and frequencies. For example, for the electrolysis process, the current density and temperature in the electrolytic cell need to be precisely controlled. The precise control of the electrolysis process can be achieved by adjusting the output frequency of the inverter. In processes such as crushing and grinding, the speed of the equipment can be controlled by adjusting the frequency of the inverter to adapt to different raw materials and processing requirements. At the same time, the voltage and frequency of the output power supply are adjusted according to actual needs to meet the requirements of different process processes. This precise energy control can improve the energy efficiency of the equipment, reduce energy waste, and reduce production costs. Typical applications: Id fan, mother liquor pump, seed pump, underflow pump, dissolution pump, feeding pump, etc.
High-voltage inverters can convert input DC power (usually AC power from the power grid converted to DC power by a rectifier) into AC power with adjustable frequency and voltage. This AC power can be applied to various non-ferrous metal production and processing equipment, such as electrolytic cells, crushers, mills, etc. By adjusting the output voltage and frequency of the inverter, the operating speed, current density and other parameters of the equipment can be controlled. The inverter adopts multi-level technology of power unit series connection to meet the needs of load speed regulation, energy saving and improved production process.
The application principle of high-voltage inverters in the non-ferrous metal industry mainly involves power control, frequency regulation and energy efficiency optimization. By accurately controlling the voltage and frequency of the output power supply, precise control of production equipment can be achieved, improving production efficiency, reducing energy consumption and improving product quality. During the production process, the motor is started and stopped smoothly, reducing the impact and stress of the mechanical system, thereby extending the service life of the equipment and reducing maintenance costs.
Compared with traditional fixed-rate control systems, high-voltage inverters are more expensive, including the cost of the equipment itself as well as the cost of installation and commissioning. This may limit some companies from adopting this technology. The installation, commissioning and maintenance of high-voltage inverters require certain expertise and skills, and the requirements for operators are high. At the same time, regular maintenance and inspection are also required to ensure the normal operation of the equipment.
Although high-voltage inverters have many advantages in the non-ferrous metals industry, such as improved energy efficiency, precise control and flexibility, they also have some disadvantages, such as high cost, high technical requirements and potential failure risks. Enterprises need to consider the advantages and disadvantages when adopting this technology. ZONCN has been deeply involved in the field of inverters and launched the latest and best products. If you have any needs, please contact us.