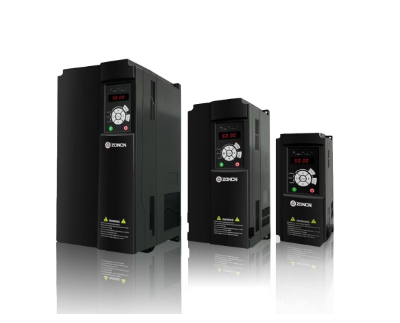
We all know that the use of frequency converter environment temperature rises 10 ℃ each, the use of life will be halved. Therefore, in the daily use, should be based on the actual use of the frequency converter environmental conditions and load characteristics, the development of a reasonable inspection cycle and system, after each use cycle, comprehensive maintenance of the frequency converter as a whole of the dismantling, inspection, measurement, etc.. Today we will tell you how to maintain the frequency converter after we use it!
According to the actual environment, determine the length of its cycle interval, comprehensive inspection and maintenance of the frequency converter. If necessary, disassemble, inspect, measure, dust and fasten the circuit boards in the rectifier module, inverter module and control cabinet. The lower air inlet and upper air outlet of the inverter are often blocked due to dust accumulation or excessive dust accumulation. Its own heat dissipation is high, requiring a large amount of ventilation, after running for a certain period of time, its substrate (electrostatic effect) with dust, must be cleaned and inspected.
Inverter circuit board inspection: for inverter circuit boards, buses and other after the necessary anti-corrosion treatment, coated with insulating paint, the emergence of partial discharges, arcs of the bus for burr removal, insulation treatment. Insulation damage to the insulation column, must be removed carbonized or replaced. Carefully inspect the electronic components on the inverter control circuit board, check and deal with abnormalities such as welding off, discoloration, swelling, cracks, broken wires (printed circuit board lines), and if necessary, the abnormal appearance of the components can be inspected or replaced from the circuit board.
The rotation status of the fan in the inverter should be carefully checked. After power failure, rotate the fan blades by hand and observe whether the bearings are stuck or rotating inflexibly, and replace them if necessary.
Use multimeter, bridge and other instruments and tools to test the rectifier block, inverter GTR (or IGBT) and other large-carrying devices, measure their positive and negative resistance values, and make a table record, and replace the modules with large differences in parameters.
Check the main contactor and other auxiliary relays, carefully observe whether there are arcs, burrs, surface oxidation, bumps on the movable and static contactors of each contactor, and replace the corresponding movable and static contactors when these problems are found to ensure contact safety.
Reasonable design of the load, avoid overload operation, as well as too high or too low operating temperature. Install appropriate protection equipment, such as over-current protection, over-voltage protection, overload protection, etc., to ensure that the frequency converter works properly within the design specifications, to avoid the impact of large currents on the impact of the frequency converter, affecting the normal operation.
Frequency converter has the advantages of wide speed range, fast dynamic response, high speed accuracy, perfect protection function, simple operation, etc. It is widely used in metallurgy, petrochemical industry, electric power, machinery, civil electric appliances and other industries. Generally speaking, the frequency converter is used for about 7 years, and enters into a fault-prone period, and fault phenomena such as burnt-out parts, malfunction, and frequent action of the protection function may occur, which seriously affects the normal operation. By taking the above measures, we can effectively extend the service life of the inverter, improve its reliability and stability, and reduce the downtime and maintenance costs caused by unexpected failures.