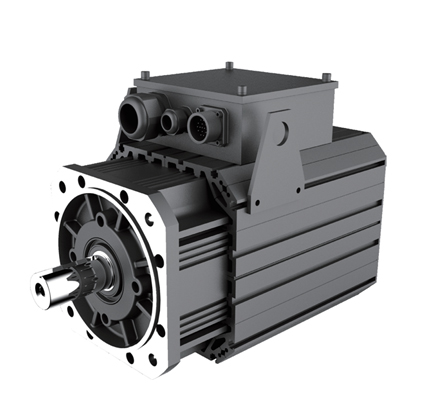
An electric motor is a device that converts electrical energy into mechanical energy and is widely used in various fields such as industry, commerce, household appliances, and transportation. The working principle of electric motors is based on the law of electromagnetic induction and the law of electromagnetic force. When electric current passes through the coils of a motor, a magnetic field is created. This magnetic field interacts with the permanent magnets or electromagnets inside the motor to create torque, which drives the motor’s rotor to rotate. This rotational motion can be used to drive mechanical loads and convert electrical energy into mechanical energy.
Frequency converters are mainly used to drive and control AC motors, especially the following types of motors:
1. Induction Motor
Three-Phase Induction Motor: Most commonly used, suitable for industrial and commercial applications, offering ruggedness and reliability.
Single-phase induction motor: Commonly used in small household appliances and light industrial equipment.
Features:
Simple structure: no brushes and commutator, low maintenance cost.
Strong adaptability: suitable for frequency converter control and can operate in a wide range of speeds.
High efficiency: High efficiency especially in high power applications.
2. Synchronous Motor
Permanent Magnet Synchronous Motor (PMSM): used in applications requiring efficient and high-precision control, such as electric vehicles and precision machinery.
Brushless DC Motor (BLDC): Commonly used in small equipment and household appliances, such as fans and power tools.
Features:
High precision: Speed and position control have high precision, suitable for high dynamic response applications.
High Performance: Excellent in both constant speed and variable speed applications.
3. Special type motors
Servo Motor: Used in applications that require precise control of position, speed and torque, such as robots and CNC machine tools.
Variable Speed Motor: Specially designed to be used with a frequency converter to optimize performance.
Features:
Precise control: Provides highly controllable output, suitable for complex and precise control tasks.
Rapid response: Quickly respond to control instructions and adapt to dynamically changing loads.
Selection of motors suitable for frequency converters
Consider the following factors when selecting an electric motor:
- Application requirements: Choose the appropriate motor type according to the specific application, such as synchronous motors for high-precision control applications and induction motors for broad industrial applications.
- Power and load characteristics: Ensure that the rated power and load characteristics of the motor match the frequency converter to ensure stable and efficient operation of the system.
- Environmental conditions: Consider environmental factors such as temperature, humidity and protection level, and select a motor that adapts to the environment.
- Control accuracy and dynamic response: For applications requiring high accuracy and fast response, choose servo motors or permanent magnet synchronous motors.
Applications
Industrial production lines: Use three-phase induction motors and frequency converters to control the speed of conveyor belts, pumps and fans to improve production efficiency and save energy.
Electric vehicles: Use permanent magnet synchronous motors and frequency converters to achieve efficient power control and recycle braking energy.
Household appliances: Inverters work with single-phase induction motors or brushless DC motors to improve the performance and energy-saving effects of home appliances such as air conditioners and washing machines.
Summarize
Frequency converters are mainly used to drive induction motors, synchronous motors and some special types of motors. Depending on the needs of the specific application, selecting the appropriate type of motor and frequency converter combination can achieve efficient, precise and reliable motor control.