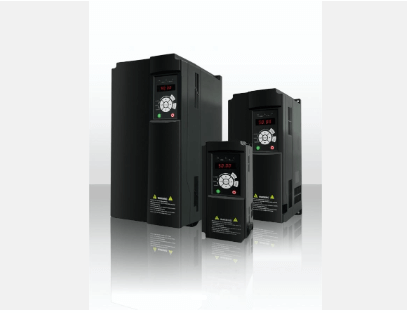
Control systems are ubiquitous in industrial, medical, military, automotive, utility, and many other applications, and we can see them even in our daily lives.
PID controllers adjust various process variables (such as temperature, speed, pressure, flow, etc.) to achieve and maintain them near setpoints (target values). PID controllers minimize the deviation between the process variable and the setpoint by continuously adjusting the control input.
PID controllers are a control loop mechanism that uses feedback and are widely used in industrial control systems and various other applications that require continuous modulation control. In actual applications, there are many different types of controllers. However, the most popular controller is the PID controller. PID stands for “proportional, integral, derivative”. The PID loop changes its output to achieve the desired setpoint with minimum error and optimal speed, which overcomes the shortcomings of other control types, making it an indispensable tool in various engineering and technical applications.
The PID controller algorithm is a feedback control algorithm used in automatic control systems, which aims to adjust the process variable (such as temperature, speed, position, etc.) to a set target value (setpoint). The PID controller algorithm achieves this by calculating the proportional, integral, and derivative outputs. As the PID loop runs, it calculates an “error” value, which is the difference between the measured process variable and the desired setpoint. The controller then adjusts the control variable to minimize the error over time.
PID controller algorithms are used in a wide variety of industrial control systems, including:
- Temperature control systems (e.g. HVAC, industrial furnaces)
- Speed control systems (e.g. motor control)
- Position control systems (e.g. robotics, CNC machine tools)
- Flow and pressure control systems (e.g. pipeline transportation)
What are the types of controllers?
What is an open-loop controller?
Open-loop control – the most basic type. It operates the control system according to pre-set instructions, without regard to the influence of the system output (i.e. the actual result). An example is a household toaster. The toaster heats the bread for a set time, regardless of the actual temperature of the bread. It stops heating at the end of the set time, regardless of whether the bread has reached the desired degree of doneness. The toaster has no feedback mechanism to “close the loop” for automatic regulation.
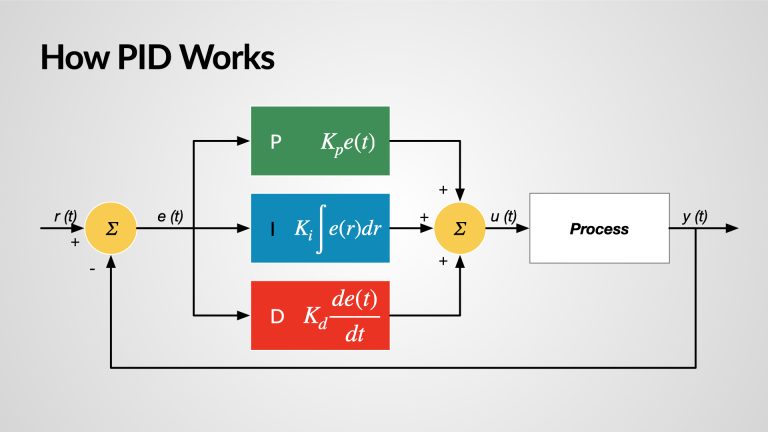
What is an on/off controller?
On/off control, which is the simplest form of closed-loop control, is a household thermostat. When the room temperature is below the set temperature, the thermostat turns the heater on (ON); when the room temperature reaches or exceeds the set temperature, the thermostat turns the heater off (OFF).
Real thermostats have hysteresis or deadband. For example, when the set temperature is 25°C, the hysteresis is usually 3-4°C, so the thermostat is on at 22°C and below, and off at 28°C and above. Due to the hysteresis of the switching action, the system is prone to oscillation or overshoot.
Without hysteresis, frequent switching operations may cause wear of actuators (such as relays). On the contrary, if the hysteresis gap is too large, it is difficult for the room temperature to maintain the optimal state most of the time.
On/off controllers are widely used in many simple automatic control systems due to their simplicity and low cost, but more complex controllers such as PID controllers are usually selected in situations where high accuracy and stability are required.
What is a PID controller?
PID control is a continuous control method that provides more detailed, stable and higher quality performance than the relatively crude on/off method. PID control is widely used in the industrial field. About 95% of closed-loop systems in industrial automation use PID controllers. PID controllers are most widely used in process industries, where PID controllers can maintain consistency of important variables.
The three major applications of PID controllers are temperature control, pressure control and flow control. Chemical, oil and gas industries and power industries use PLCs to control these parameters.
In an industrial temperature control system, such as a heat treatment furnace, a PID controller is used to maintain the furnace temperature at a set value (such as 700°C). The system achieves the set temperature by measuring the actual furnace temperature (process variable), comparing it to the set value, calculating the error, and adjusting the power of the heating element according to the control output calculated according to the PID algorithm.
PID controllers are widely used in various automatic control systems due to their simplicity, flexibility and wide applicability. From temperature control, speed control to position control and flow control, PID controllers play an important role in industrial automation, home appliances, robotics, aerospace, etc. By properly adjusting the PID parameters, system performance can be optimized to achieve high-precision and high-efficiency control.