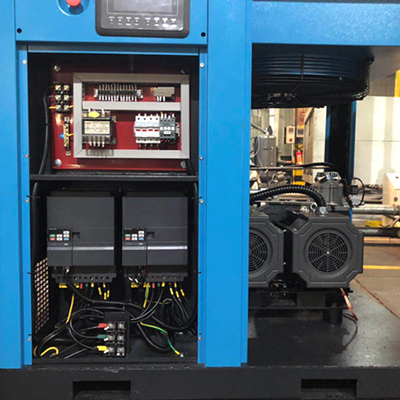
Air compressors, sometimes also called pneumatic compressors. As a power source, air compressors extract energy from pressurized air and use it to drive pneumatic tools. Any tool can be dangerous if not used properly, and the best way to ensure safety is to use an air compressor of the right size.
Our advice is to find the highest air pressure and air delivery requirements of your pneumatic tools, and then choose a compressor model that exceeds these requirements. For example, if you have a compressed air drill that requires 10 CFM and 100 PSI, then we can choose a 15CFM pneumatic compressor.
Of course, the larger the air compressor, the more powerful it is. Some seemingly large air compressors have low air output, but some compact air compressors have high air output. There are many factors that affect the performance of air compressors, and we need to consider many aspects.
7 things to consider when choosing an air compressor
1. The purpose and demand of the air compressor
First, we need to clarify the specific purpose of the air compressor and the amount of compressed air required. Because different applications (such as industrial production, automobile maintenance, construction, etc.) have different requirements for air compressors.
2. Air Delivery Volume
One of the most important considerations when purchasing a new air compressor is the amount of air flow the compressor is capable of delivering. Air tools have certain requirements in order to operate at optimal capacity. More important is the required SCFM or Standard Cubic Feet Per Minute.
Generally speaking, air compressors with lower CFM ratings are suitable for passenger car tire inflation and small tools, whereas, air compressors with higher CFM ratings are designed for industrial applications, OTR tire inflation, and larger tools.
3. Compressor air tank size
While the overall size of a compressor isn’t overly important, the size of its air tank can affect air capacity and performance. Small compressed air tanks require frequent refills and won’t last as long. The size of the air tank depends on the peak demand of the system and how often the air compressor is started. A larger air tank can reduce the number of times the air compressor is started, thereby extending its life.
Construction crews need larger, higher-pressure air compressors. Large models have tank capacities ranging from 1 gallon to 80 gallons. Generally speaking, most crews should keep their tank capacities around 20 gallons, as large air compressors are more difficult to store.
4. Power
Air compressor power considerations include horsepower and power source. Horsepower indicates the power provided by the unit’s engine, and air compressor power options include electric, hydraulic, and gas. While more horsepower (HP) doesn’t always mean a more powerful compressor, it’s a factor worth considering.
5. Oil-free or oil-free compressors
Oil-free compressors are low-maintenance and free of contaminants. Standard oil-based compressors have greater output power and run more quietly.
6. Air compressor life cycle
Consider the frequency of use and working hours of the air compressor. If the air compressor needs to run continuously for a long time, you need to choose a more durable and higher-performance model.
7. Frequency converter in the air compressor
The frequency converter (variable frequency drive, VFD) in the air compressor plays a vital role. The frequency converter can automatically adjust the operating speed of the air compressor according to the changes in air consumption, avoid frequent starting and stopping of the air compressor, and reduce energy consumption.
The specific selection steps are as follows:
- Calculate the total air demand: determine the air consumption of all equipment that requires compressed air, and add a certain margin.
- Determine the working pressure: select the appropriate working pressure according to the requirements of the equipment used.
- Select the appropriate air tank: select the appropriate air tank size according to the peak demand of the system.
- Select the type of air compressor: select the appropriate type of air compressor (such as piston, screw, centrifugal, etc.) according to the usage scenario.
- Evaluate energy efficiency and cost: consider the energy efficiency rating and total cost of the air compressor, including the initial purchase cost and long-term operating cost.
- Consider the brand and after-sales service: Choose a brand with a good reputation and after-sales service.
By considering these factors comprehensively, you can choose the size and model of air compressor that suits your needs. If there are specific demand parameters, you can provide more details so that more specific suggestions can be given.